Your cart is currently empty!
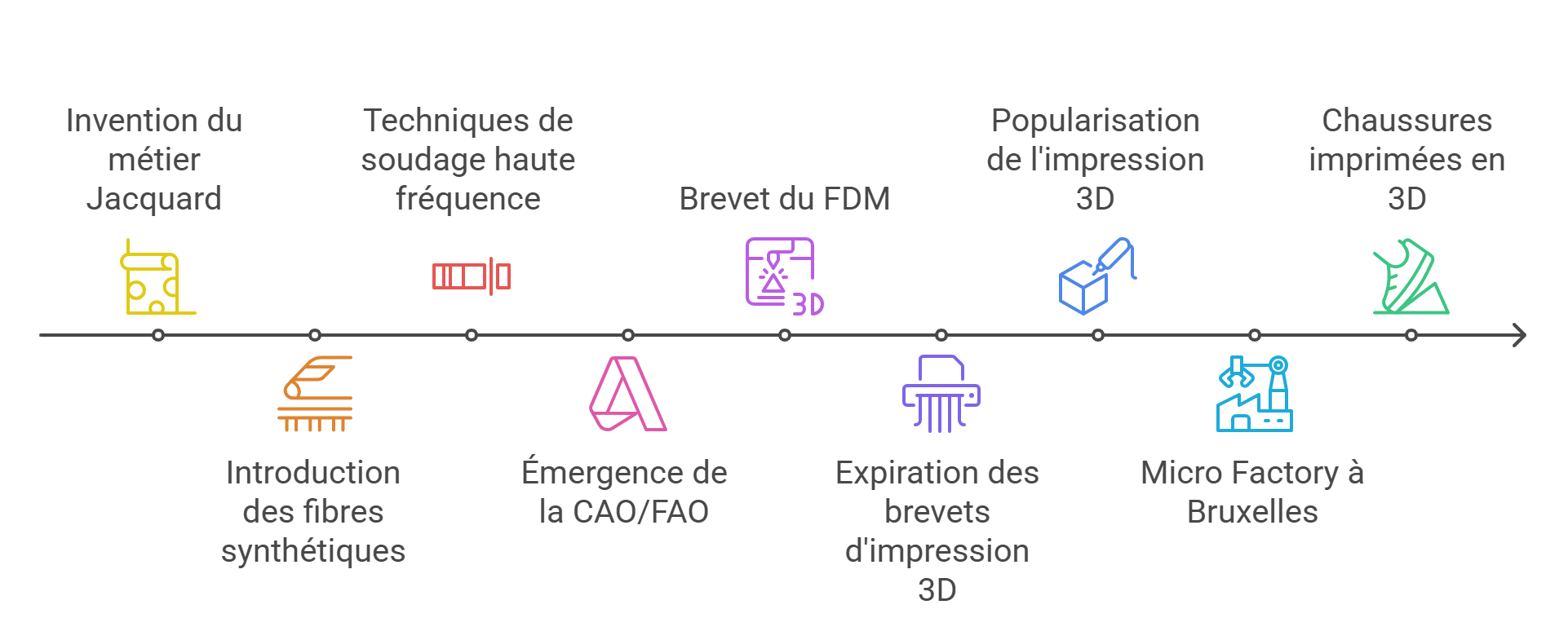
Étude : Textiles techniques et de l’impression 3D
Du métier Jacquard à l’impression 3D : un continuum historique, socio-politique et durable
Du métier Jacquard à l’impression 3D : une continuité historique et technique
Introduction
L’histoire du textile est marquée par une évolution continue, du métier Jacquard jusqu’à l’émergence de l’impression 3D. Loin d’être une rupture brutale, cette transition s’est construite par étapes successives, mêlant innovation technologique, adaptation sociale et recherche de durabilité.
Aujourd’hui, l’impression 3D textile représente une avancée stratégique majeure, offrant des possibilités uniques pour la personnalisation, la relocalisation de la production, et la réduction de l’impact environnemental. En Europe, cette technologie ouvre la voie à des micro-usines et des modèles de fabrication hyper-locale, favorisant une nouvelle dynamique économique ancrée dans l’économie circulaire.
Des racines mécaniques à l’ère électronique : du métier Jacquard à la CNC
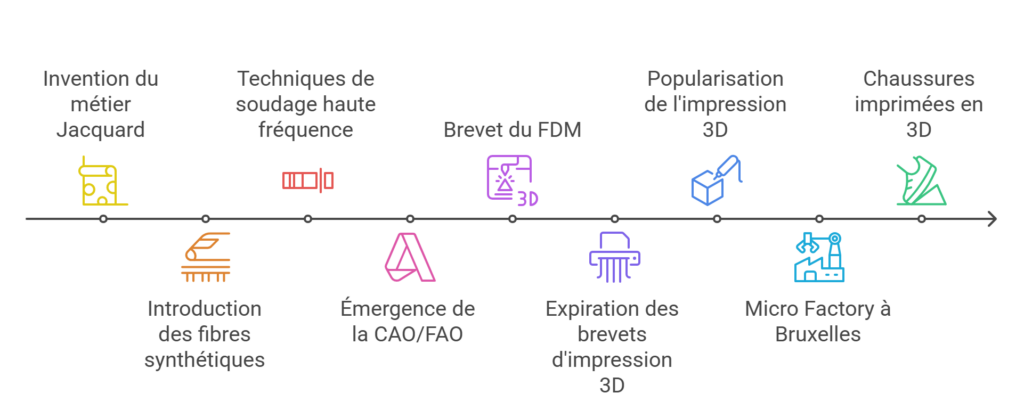
Le métier Jacquard, précurseur de la programmation
L’invention du métier Jacquard, au début du XIXᵉ siècle (1804), a révolutionné le tissage. Son système de cartes perforées permettait de « programmer » des motifs complexes en automatisant le contrôle de fils de chaîne. Au-delà du gain de productivité, il s’agit du premier jalon d’une « numérisation » du textile : cette logique binaire de lecture des cartes anticipe l’idée de contrôle informatique, tout en marquant une première rupture avec le geste exclusivement manuel.
De la mécanisation à l’électronique
Au fil du XXᵉ siècle, les métiers à tisser et à tricoter ont intégré des systèmes de plus en plus sophistiqués : moteurs asservis, capteurs, pilotage par ordinateur. Les outils de CAO/FAO (Conception et Fabrication Assistées par Ordinateur), qui ont émergé dans les années 1970 et 1980, se sont imposés dans la broderie industrielle et la découpe de tissu, ouvrant la voie à une personnalisation plus fine.
Parallèlement, l’expansion de la production textile à grande échelle s’est accompagnée d’une délocalisation massive, en particulier vers l’Asie, surnommée « usine du monde ». Cet essor, toutefois, a entamé une mutation : plusieurs régions asiatiques, comme Shenzhen, ont évolué vers une industrie à plus forte valeur ajoutée, investissant dans l’automatisation et l’innovation (robotique, impression 3D). Sur le plan socio-politique, ce recentrage révèle comment la maîtrise technologique devient un levier stratégique pour dominer la chaîne de valeur du textile.
Une nouvelle vision : Micro-usines et Nanofabs
Dans une démarche visant à réconcilier artisanat et modernité, les concepts de Micro Industrie et de Nanofabs proposent une nouvelle approche de la production. Inspiré par des initiatives comme la Micro Factory à Bruxelles, qui partage certaines caractéristiques mais reste un projet distinct, le terme Nanofab, tel qu’il est utilisé ici, désigne une proposition spécifique de micro-usines spécialisées. Ces structures associent savoir-faire artisanal et technologies modernes, comme l’impression 3D textile, en optimisant les ressources et les processus pour répondre de manière spécifique et durable aux besoins locaux. Cette hybridation permet d’allier créativité, précision et respect des principes de durabilité. Contrairement aux FabLabs, où les outils sont polyvalents, les Nanofabs se concentrent sur des chaînes de production hyper-spécialisées, garantissant une optimisation technologique pour des usages précis. Cette approche vise à maximiser l’impact positif de la fabrication locale tout en réconciliant progrès technologique et durabilité environnementale.
(article sur ” Micro Industrie et Nanofabs”)
L’avènement des textiles techniques : diversification et nouvelles propriétés
Matériaux synthétiques et composites
L’introduction de fibres synthétiques (nylon en 1935, polyester dans les années 1940, aramide, etc.) a radicalement modifié l’offre et les usages dans le textile. Plus solides, moins sujettes aux aléas climatiques, ces fibres ont ouvert la voie à des applications exigeantes : aéronautique, sport de haut niveau, dispositifs médicaux.
Progressivement, les textiles enduits ou composites (association fibre + matrice polymère) ont accru leur performance (résistance, étanchéité, légèreté). Les gilets pare-balles à base de fibres aramides ou les toiles tendues architecturales sont autant d’exemples qui soulignent l’importance stratégique des recherches en chimie des polymères.
Du savoir-faire traditionnel à la haute technologie
Dans ces nouveaux secteurs, la haute performance s’accompagne d’un besoin accru de spécialisation. Tandis que la main-d’œuvre peu qualifiée a vu ses tâches répétitives menacées par l’automatisation, les compétences se sont polarisées vers la R&D, la maintenance, le design et la programmation. Cette transition, si elle crée des opportunités, peut aussi accentuer les inégalités si la formation ne suit pas. Ainsi, des programmes de recyclage professionnel et de montée en compétence sont devenus essentiels pour accompagner la main-d’œuvre vers ce « textile technique et numérique ».
De la couture au soudage : la révolution discrète de l’assemblage
Soudage haute fréquence, ultrasons et lamination
Historiquement, la couture fut l’élément central de l’assemblage textile. Mais l’apparition de matériaux enduits ou thermoplastiques a fait émerger d’autres procédés : soudage à haute fréquence (HF) dans les années 1940-1950, par ultrasons ou par air chaud.
- Solidité accrue : L’absence de perforation par l’aiguille supprime un point de faiblesse.
- Étanchéité : La fusion des couches polymères crée un joint hermétique.
- Rationalisation : Moins de surépaisseurs, donc un gain de poids et une amélioration de la durabilité.
Ces techniques ont précédé l’idée de déposer du matériau (colle, film polymère) pour assembler des pièces, préfigurant la logique de la fabrication additive par fusion couche à couche.
La couture, un savoir-faire toujours présent
Si le soudage et la lamination se sont imposés dans les textiles techniques, la couture n’a pas disparu pour autant. Certains segments (maroquinerie, mode de luxe) valorisent le geste artisanal et la qualité perçue de la couture. De même, la couture reste essentielle pour des combinaisons de matériaux non thermoplastiques. L’évolution se fait donc moins par substitution totale que par un enrichissement du panel d’outils de production, selon les usages et les contraintes.
L’impression 3D textile : vers une révolution durable ?
De la « hype » à la spécialisation sectorielle
À l’aube des années 2010, l’impression 3D a suscité un engouement massif, souvent présentée comme la prochaine révolution industrielle. Dans la pratique, elle s’est développée d’abord dans des niches à haute valeur ajoutée (médical, aéronautique, bijouterie).
De la même manière, l’impression 3D textile ne prétend pas remplacer toutes les méthodes existantes. Elle vise plutôt des applications qui requièrent une personnalisation (chaussures moulées sur mesure, orthèses médicales), une complexité géométrique (structures maillées inspirées du tissage) ou une production hyper-locale (petites séries, modèles exclusifs).
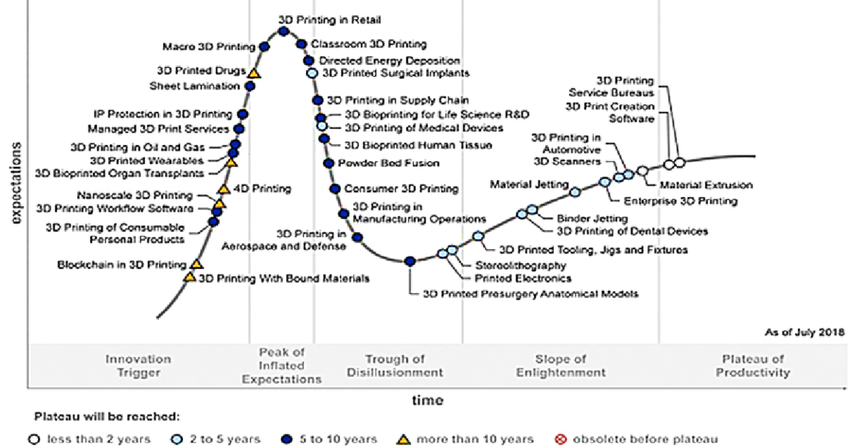
Une continuité entre tissage et soudage
Le FDM (Fused Deposition Modeling), breveté en 1989 par Scott Crump, illustre particulièrement cette synthèse :
- Tissage : Déposer un fil polymère de façon contrôlée, couche après couche, rappelle la logique de la trame et de la chaîne.
- Soudage : Chaque passage de buse « soude » instantanément le nouveau filament à la couche précédente, créant une pièce monobloc.
Les projets comme DefeXtiles, qui créent des textiles quasi-tissés par sous-extrusion, ou les expérimentations sur tulle (où les filaments s’accrochent directement au tissu) soulignent la puissance créative de cette hybridation. Dans la mode, Danit Peleg ou Iris van Herpen en ont fait des démonstrations spectaculaires, ouvrant de nouvelles esthétiques et de nouveaux procédés de confection.
Polymères avancés et TPU moussant
Le TPU (Thermoplastic PolyUréthane), en particulier dans ses versions moussantes (Foamy, Varioshore, etc.), s’est imposé comme matériau vedette de l’impression 3D textile, avec une adoption croissante à partir des années 2010 et l’apparition du Varioshore ces dernières années :
- Flexibilité et résilience : Adaptées aux pièces portables ou amortissantes, comme les semelles de chaussures ou les accessoires sportifs.
- Densité modulable : Les paramètres d’impression peuvent créer des zones plus ou moins rigides.
- Recyclage théorique : Si le produit final est en mono-matériau, il est plus facile à retraiter ou à broyer pour réutilisation.
Des marques comme Zellerfeld, qui a lancé ses premières chaussures imprimées en 2020, proposent des solutions entièrement imprimées, facilitant la personnalisation et théoriquement le recyclage (chaussure « monobloc »). Certaines initiatives locales, comme NanoFab à Bruxelles, expérimentent les top tube bags pour vélos, combinant légèreté et design personnalisé.
Les implications socio-politiques : production locale et transformation du travail
Micro-usines et relocalisation partielle
La fabrication additive permet d’envisager la production de petites séries au plus près du consommateur. En Europe, ces structures, parfois qualifiées de micro-usines et décrites ici comme “Nanofabs” par l’auteur, offrent une réponse possible à la mondialisation en limitant les stocks et en réduisant le transport. Par exemple, des initiatives comme la Micro Factory à Bruxelles illustrent certains aspects de ce modèle. Le concept de “Nanofab” reste cependant une proposition spécifique visant à intégrer production locale et technologies avancées, déjà mentionnée comme une vision unique dans la section précédente.
- Réduction des dépendances : L’impression 3D textile peut limiter l’importation massive de produits finis depuis l’Asie, offrant une forme de souveraineté industrielle.
- Dynamique d’innovation locale : L’ancrage dans des écosystèmes (FabLabs, centres de recherche, incubateurs) favorise la création de start-ups, comme en Belgique, qui allient savoir-faire traditionnel et nouvelles technologies.
Transformation des compétences et nouveaux métiers
Le développement de l’impression 3D textile requiert des profils hybrides, alliant :
- Connaissance des propriétés des fibres et des polymères (héritage du monde textile).
- Maîtrise de la CAO et de la fabrication additive (compétences numériques).
Sur un plan socio-politique, cette mutation pose des questions sur la distribution des emplois et la formation. Dans la mesure où les tâches répétitives s’automatisent, il s’agit de former la main-d’œuvre à des métiers plus techniques et plus créatifs (design, maintenance d’équipements, programmation). À défaut, le risque de précarisation d’une partie des travailleurs existe, surtout dans les régions historiquement tournées vers la couture manuelle.
Évaluation environnementale : vers un modèle plus circulaire ?
Réduction des déchets et fabrication à la demande
L’impression 3D textile, par sa nature additive, génère peu de chutes comparée à la coupe de tissu. Sa capacité à produire « à la demande » peut également limiter les surplus et les invendus, un problème récurrent dans l’industrie de la mode. Sur ce point, l’approche peut donc contribuer à un modèle plus vertueux, surtout si l’objet imprimé reste en mono-matériau (meilleure recyclabilité).
Défis de l’empreinte énergétique et du recyclage
Cependant, plusieurs défis demeurent :
- Consommation d’énergie : Les imprimantes 3D fonctionnent souvent des heures, voire des jours, pour finaliser un produit.
- Origine pétrochimique : La plupart des polymères (TPU, ABS) sont issus du pétrole. Les filières de recyclage effectif restent limitées, même si la théorie du « mono-matériau recyclable » est prometteuse.
- Matériaux biosourcés : Des pistes existent (PLA, TPU biosourcé), mais restent à consolider pour offrir la même performance.
Le défi écologique est donc double : mettre en place des circuits de collecte et de recyclage adaptés, et encourager la recherche sur des polymères moins carbonés.
Conclusion
De la lecture des cartes perforées du métier Jacquard aux installations d’impression 3D modernes, l’histoire du textile illustre une progression constante vers des méthodes de production plus innovantes, adaptées et durables. L’impression 3D textile ne se substitue pas aux techniques traditionnelles, mais les complète en offrant des opportunités uniques de personnalisation, de production hyper-locale et de création de structures complexes.
À travers des initiatives comme NanoFab, cette technologie s’impose comme une solution stratégique pour relever les défis actuels de relocalisation et d’économie circulaire. En combinant innovation technologique et respect de l’environnement, elle offre une voie prometteuse pour les secteurs à forte valeur ajoutée, notamment dans la mode, les accessoires sportifs et les solutions de mobilité.
Cette transition n’est toutefois pas dépourvue de défis. L’adoption réussie de l’impression 3D textile repose sur une transformation des compétences professionnelles et une intégration accrue de circuits de production durables. Le développement de filières de recyclage et l’utilisation de matériaux biosourcés restent des étapes essentielles pour réaliser pleinement le potentiel de cette technologie.
L’impression 3D textile invite ainsi à réfléchir différemment aux modèles de production et de consommation. Plutôt qu’une révolution, elle propose un enrichissement de l’héritage existant, ouvrant la voie à des collaborations entre artisans, industriels et innovateurs. En adoptant une approche responsable et concertée, cette technologie pourrait devenir un pilier central d’une transition écologique et sociale, tout en favorisant la souveraineté industrielle et la créativité locale.
Recommandations pour une adoption responsable
Renforcer la formation des « artisans hybrides »
Développer des cursus associant techniques textiles traditionnelles, chimie des polymères et CAO/FAO pour former une nouvelle génération de professionnels.
Soutenir la recherche sur des matériaux plus verts
Encourager la création de filières de recyclage spécifiques et la conception de polymères biosourcés adaptés à l’impression 3D textile.
Promouvoir la production distribuée et les micro-usines
Valoriser des projets pilotes (FabLabs, nanofabs) afin de faciliter l’émergence d’acteurs locaux, soutenus par des mécanismes de financement (programmes européens, incubateurs).
Mettre en place des normes et une régulation adaptée
Établir des standards pour la qualité et la sécurité des produits imprimés, notamment dans les secteurs sensibles (médical, sport, etc.).
- Intégrer des critères environnementaux (consommation énergétique, recyclabilité) dans ces normes.
Communiquer sur les enjeux et sensibiliser
Informer les consommateurs, décideurs et industriels sur le potentiel, mais aussi les limites, de l’impression 3D textile : sa « non-révolution » est l’occasion de replacer cette technologie dans une approche plus réaliste et durable.
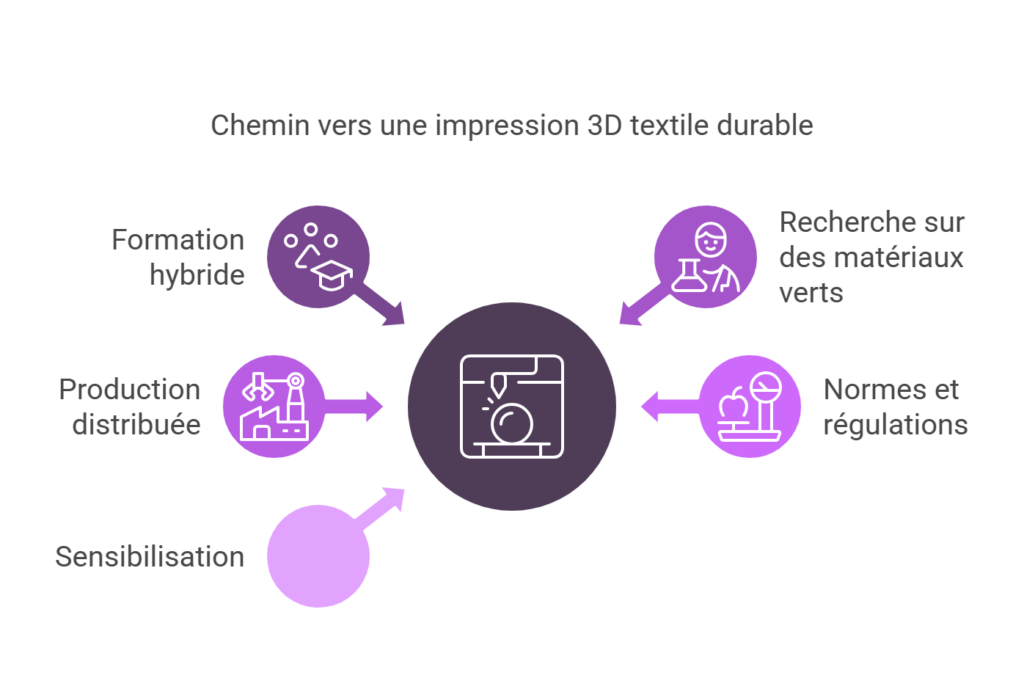
Par ce mix d’actions, l’impression 3D textile pourra se déployer de manière responsable, en s’appuyant sur le continuum historique qui l’a précédée et en tenant compte des impératifs de durabilité, de souveraineté et d’évolution du travail.